All Science News
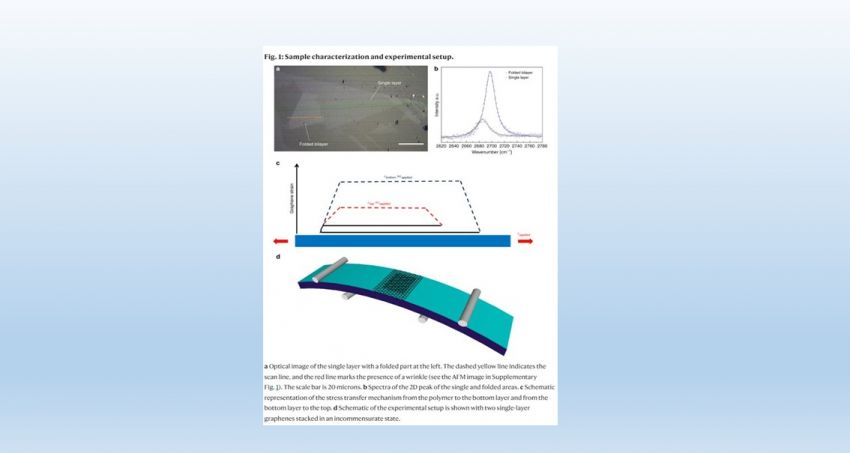
Development of superlubricity in graphene materials.
Researchers of FORTH / ICE-HT in Patras headed by Prof. Costas Galiotis of Chemical Engineering Dept. of University of Patras published in the high-impact scientific journal Nature Communications a scientific report for the superlubric behaviour (approximately zero friction) between two randomly packed graphene monolayers. This finding is already being tested in electrical switches and has the potential to be used in applications in aerospace and wind turbines.
The relevant article (https://www.nature.com/articles/s41467-020-15446-y) is entitled:
“Tunable macroscale structural superlubricity in two-layer graphene via strain engineering”,
Nature Comms, 11: Article number: 1595 (2020)
by Charalambos Androulidakis, Emmanuel N. Koukaras, George Paterakis, George Trakakis & Costas Galiotis
SUMMARY
Superlubricity is the state of matter of ultra-low friction. Graphite, for example, is a well-known lubricant due to its layered structure. A long-standing bottleneck for graphite is that its superlubric behaviour breaks down when its lateral dimensions exceeds a few microns (~10 μm). This is a result of the large commensurate stacking domains present at macro-scale samples that induce mechanical interlocking and inhibit the facile shearing between individual graphene layers. In our Nature Communications publication (https://www.nature.com/articles/s41467-020-15446-y) it is shown experimentally, that the above limitations can be overcome in incommensurate graphene/graphene systems by mechanical manipulation. By randomly stacking one layer graphene over another and by the application of a small initial tensile strain, the two graphene layers practically slide in respect to each other, as measured at the macro- scale. These results have important implications for practical applications and are already being tested for dry lubrication into mechanical drive components and have the potential to be used in electromechanical systems (MEMS/NEMS), electrical switches, aerospace and wind energy applications.